Continuous optimization of drilling and completion in challenging areas
INPEX is applying the latest drilling and completion technologies to minimize the environmental impact of well drilling activities while achieving more efficient operations for drilling and completion, as well as aiming to develop Oil and gas fields in frontier areas characterized by more technically challenging environments. Here are some examples of our drilling and completion initiatives:
Application of RMR (Riser-less Mud Recovery) system in offshore drilling
The shallow formations near the seabed are often unconsolidated or soft, and conventional drilling methods can lead to formation damage and lost circulation. As water depth increases, the hydrostatic pressure of the drilling mud (which has a higher density than seawater and forms a mud cake on the borehole wall to prevent collapse) from the drilling rig to the seabed can place significant stress on weak formations.
Therefore, in the drilling interval just below the seabed (called the surface hole), it is common to drill without using a marine riser (a large-diameter pipe for circulating mud from the seabed to the rig at surface). However, this method results in discharging mud onto the seabed. While we use mud with environmentally friendly additives derived from natural materials, this approach is less effective at maintaining borehole stability compared to pumping mud to the drilling rig. In addition, extension of the drilling period increases the amount of discarded mud, leading to higher costs.
In several of our projects, we have applied the RMR system, which enables mud circulation without a marine riser by pumping recovered mud from the seabed to the rig at surface. This allows us to drill the surface hole using high-quality mud without disposal, reducing problems caused by borehole instability while minimizing costs and environmental impact.
INPEX pioneered the introduction of this technology during the third exploration drilling campaign of the Ichthys Project in Australia in 2007, and we continue to utilize it as of 2024.
Courtesy of Enhanced Drilling (Case Study RMR® 5 – INPEX, Browse Basin |Enhanced Drilling)
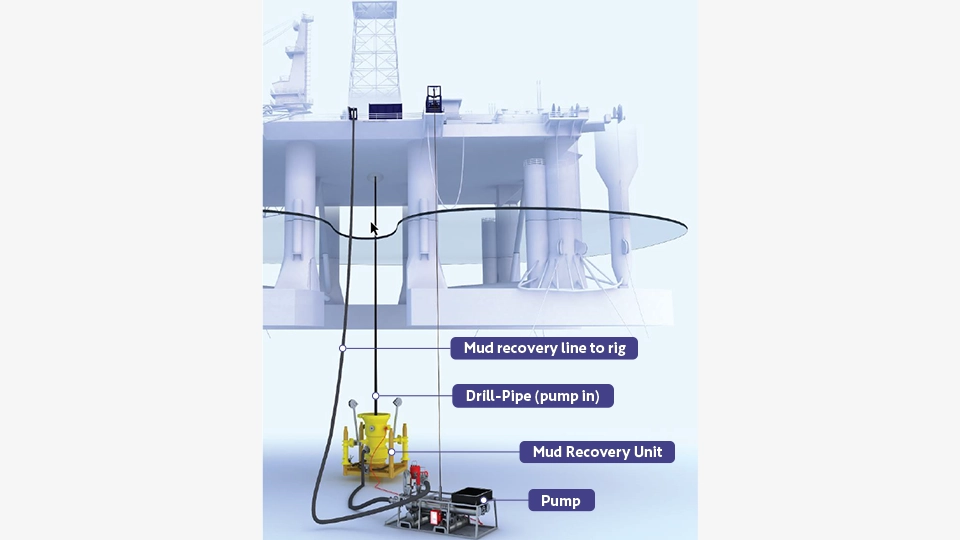
Application of MPD (Managed Pressure Drilling) system
When drilling a well, it is essential to maintain borehole wall integrity without fracturing the formation or allowing formation fluids to enter the wellbore. In conventional drilling methods, this state is maintained by adjusting the weight of the drilling mud. However, if the hydrostatic pressure of the mud is too high, it can cause fracture and lost circulation of wellbore fluids into the formation. Conversely, if the hydrostatic pressure of the mud is too low, it can lead to formation fluid influx into the wellbore or borehole collapse due to imbalanced stress.
These upper and lower limits are called the mud window, and the mud weight (hydrostatic pressure) in the wellbore must be maintained within this range (see figure below). In general, a section is drilled within a range that ensures a sufficient mud window, then isolated using a steel pipe called casing before drilling the next section with a different mud weight, again within the mud window range.
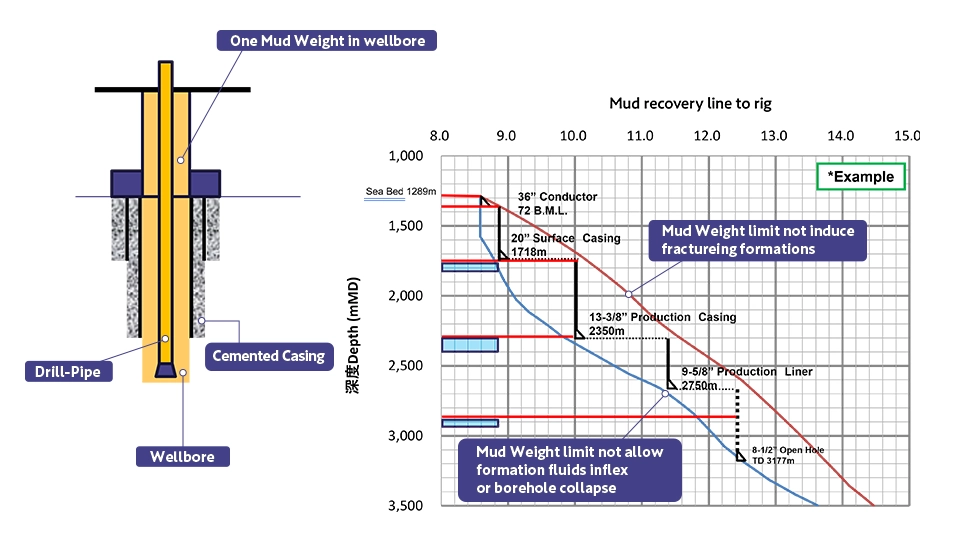
Equivalent Circulating Density, ESD = Equivalent Static Density, SBP = Surface Back Pressure)
The shape and range of this mud window vary by region, field, or even individual wells. In cases where it is particularly narrow, it becomes necessary to divide the well into smaller sections. However, there are limitations to the size and number of casings that can be inserted (as the borehole diameter progressively decreases).
In addition, when circulating mud, friction pressure (back pressure) occurs, increasing the pressure in the wellbore compared to static conditions. In cases of extremely narrow mud windows, even if the pressure is within the window under static conditions, it may exceed the upper limit once circulation begins, making drilling a challenge.
One solution to this issue is the MPD (Managed Pressure Drilling) technique, where the mud weight itself is reduced, and drilling is conducted while adjusting back pressure by applying a choke at the wellhead outlet (see figure below: ECD = Equivalent Circulating Density, ESD = Equivalent Static Density, SBP = Surface Back Pressure).
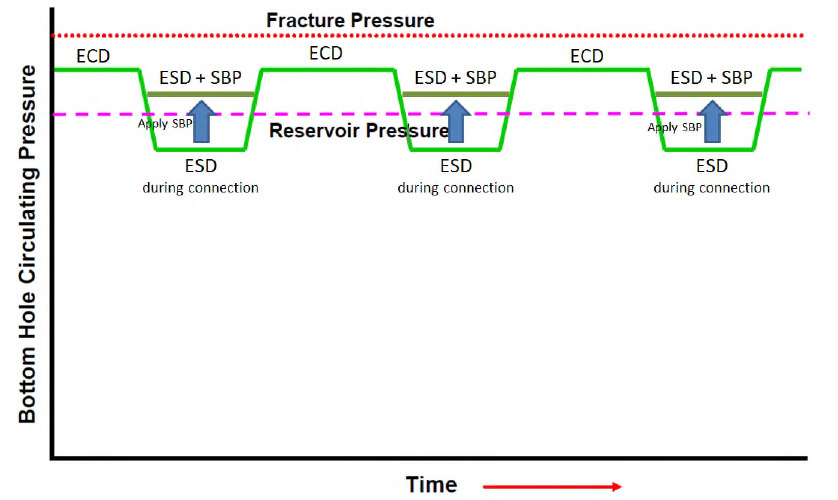
Conceptually, it is like attaching a rubber stopper (Rotating Control Device: RCD) to the mouth of a bottle, with the drilling pipe passing through the stopper. The pipe can rotate and move up and down when force is applied, but the mechanism maintains a seal to prevent liquid leakage. Below the rubber stopper is an outlet, and the back pressure is adjusted by controlling the opening size of a valve downstream (MPD choke manifold).
In conventional drilling methods, the influx or loss of drilling fluid is monitored by managing the volume-based flow rates of mud pumped into and returned from the wellbore. However, the MPD system is equipped with a Coriolis mass flow meter, allowing for extremely accurate and real-time measurement of mud inflow and outflow rates and density. This enables quick responses to even slight changes in wellbore conditions.
INPEX has been applying this MPD technology since the exploration drilling campaign in the deep-water S block offshore Sabah, Malaysia, in 2014. As of 2024, we continue to utilize this technology in wells with narrow mud windows that make it a challenge to drill the wells.
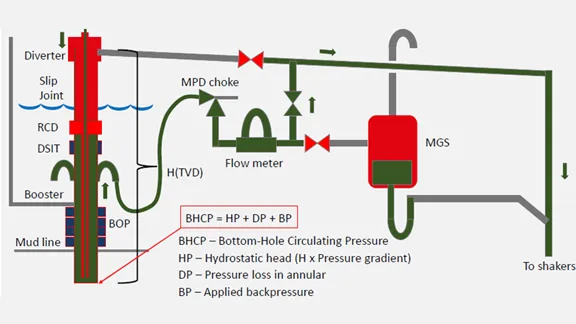
Application of ERD (Extended Reach Drilling) technology
While various technologies / techniques are necessary to drill wells vertically to great depths, there are different technical challenges in drilling horizontally over long distances. When surface restrictions prevent placing the drilling site directly above the target, drilling must start from a distant location. In addition, the shapes of Oil and gas-bearing reservoirs vary. In cases where they are thin but extensive, vertical drilling alone may not secure sufficient commercial production capacity, necessitating drilling horizontally or at near-horizontal angles for long distances within the Oil and gas layer.
Extended Reach Drilling (ERD) is a technique used to drill wells with high inclination angles towards underground structures (traps) that contain oil and natural gas, extending further horizontally. ERD wells are generally defined as those with a horizontal displacement (step-out) to vertical depth ratio exceeding 2:1.
When drilling high-angle wells over long distances, the drill pipe tends to lie on the lower side of the wellbore due to its weight, increasing the contact area with the borehole wall and thus increasing friction. The mud pump load for removing drill cuttings also increases. To overcome these challenges, high-strength pipes and drilling equipment with high-power drive capabilities are required. Moreover, meticulous planning backed by various simulations and high technical skills to execute these plans reliably are essential.
Our company has drilled numerous ERD wells in locations such as Abu Dhabi and Australia (see figure below: Global ERD wells and our performance in Abu Dhabi fields). We have also achieved a world record for the longest ERD well at an oil field in Abu Dhabi in which we have a participating interest (drilling length: 15,540 m, as of 2023).
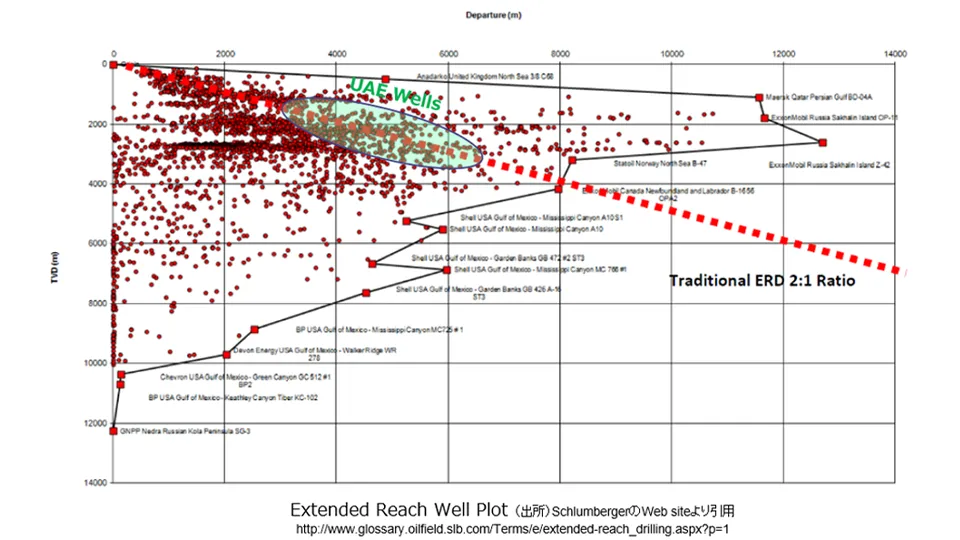
Development of Multi-Lateral Tie-Back System (MLTBS - TAML Level-5) technology
Multi-lateral completion technology refers to the technique of drilling multiple lateral wells from a single wellbore and completing them for efficient production. Based on an idea from our drilling engineers, JODCO (now INPEX Abu Dhabi Business Unit), JNOC-TRC (now JOGMEC-TRC) and Sperry-Sun (now Halliburton Completions) conducted joint research and developed the MLTBS TAML (Technology Advancement for Multi-Laterals) Level-5 completion technology (see figure below).
This technological development enables pressure isolation between multiple lateral wells while allowing selective and physical access by CT (Coiled Tubing: Small diameter seamless steel tubing wound on a single reel, used for well intervention operations) to each lateral at any time, making it possible to perform productivity improvement operations (interventions) on the lateral wells. In the Oil and gas development industry, it is common for major service companies to develop equipment and technologies. However, there are also instances where operators like oil majors or IOCs collaborate on the joint development of equipment and technologies based on their own ideas, or where engineers with long industry experience establish their own companies to provide technologies, equipment and services that incorporate their ideas.
SPE 101385 “Challenges, Lessons Leaned, and Successful Implementations of Multilateral Completion Technology Offshore Abu Dhabi”, Shuichi Kikuchi, SPE, and Abdulla S. Fada’q, SPE, ZADCO, Abu Dhabi, UAE
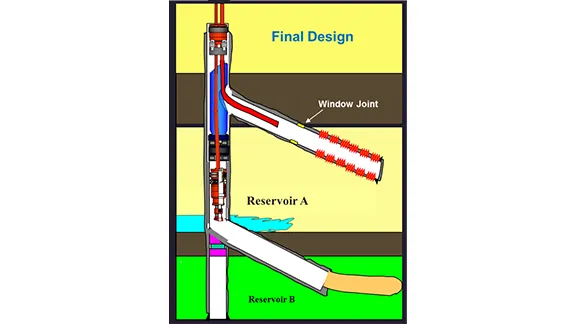